밀링 커터의 특징
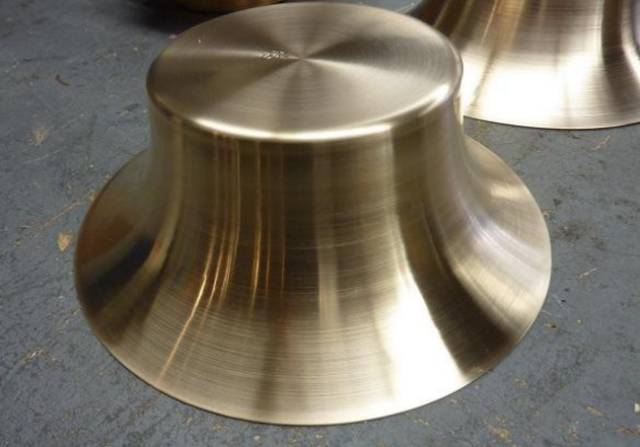
가공을 시작하기 전에 치구의 강성을 강화하려는 노력은 향후 장기 생산에 도움이 될 것입니다. 공구 수명을 연장할 뿐만 아니라 가공물의 표면 품질을 향상시키고 가공 오류를 줄여줍니다.
마찬가지로 공구 홀더를 잘못 선택하면 공구 수명이 단축됩니다. 예를 들어 커터 홀더(스프링 척 대신)에 직경 3.175mm의 엔드밀을 장착하면 조임 나사의 작용으로 인해 커터와 커터 홀더 사이의 끼워맞춤 간격이 1로 치우쳐집니다. 측면으로, 커터의 중심이 벗어났습니다. 공구 홀더의 회전 중심은 작동 중 밀링 커터의 반경 방향 흔들림을 증가시켜 밀링 커터의 각 날에 불균형한 절삭 부하를 초래합니다. 이러한 절삭 상태는 특히 니켈 기반 합금을 밀링할 때 공구에 좋지 않습니다.
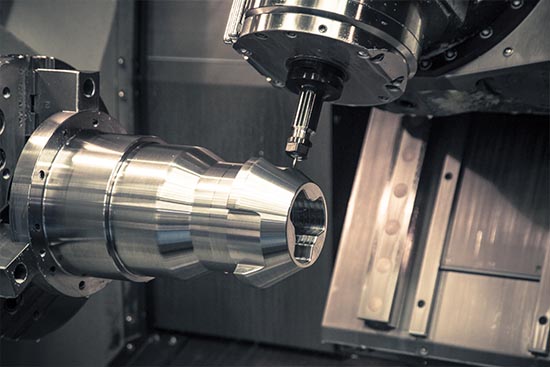
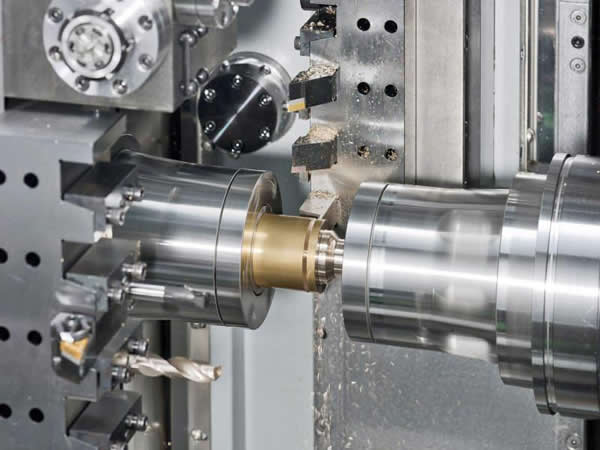
유압 척, 열박음 척 등 공구 장착 편심을 개선하는 공구 홀더를 사용하면 절삭 작업의 균형과 안정성이 향상되고 공구 마모가 감소하며 표면 품질이 향상됩니다. 손잡이를 선택할 때는 원칙을 따라야 합니다. 즉, 손잡이는 가능한 한 짧아야 합니다. 이러한 공구 및 공작물 클램핑 요구 사항은 모든 재료 밀링에 적용되며, 니켈 기반 합금을 밀링할 때는 가능한 한 고급 가공 경험이 필요합니다.
도구 사용
공구 설계 방식이나 재질에 관계없이 공구 제조업체는 절삭 속도 및 날당 이송에 대한 초기 값을 제공해야 합니다. 이러한 데이터를 사용할 수 없는 경우 제조업체의 기술 부서에 문의해야 합니다. 대부분의 표준 밀링 커터는 이렇게 많은 작업을 처리할 수 없기 때문에 제조업체는 자사 제품이 전폭 홈 가공, 윤곽 가공, 플런지 가공 또는 램핑 작업을 얼마나 잘 수행할 수 있는지 알아야 합니다. 예를 들어, 밀링 커터의 두 번째 여유각이 충분히 크지 않으면 램핑을 위한 베벨 각도가 줄어듭니다.
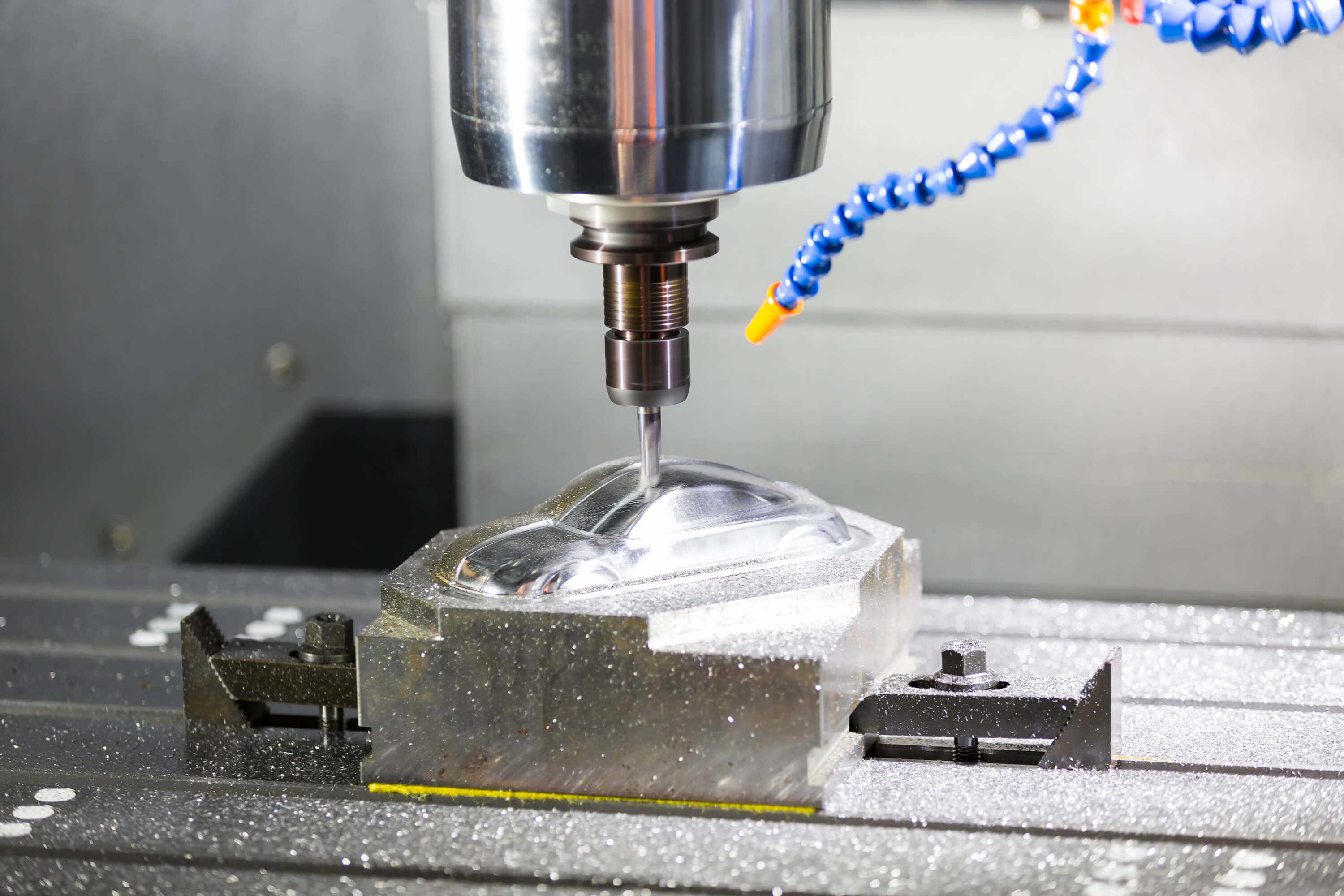
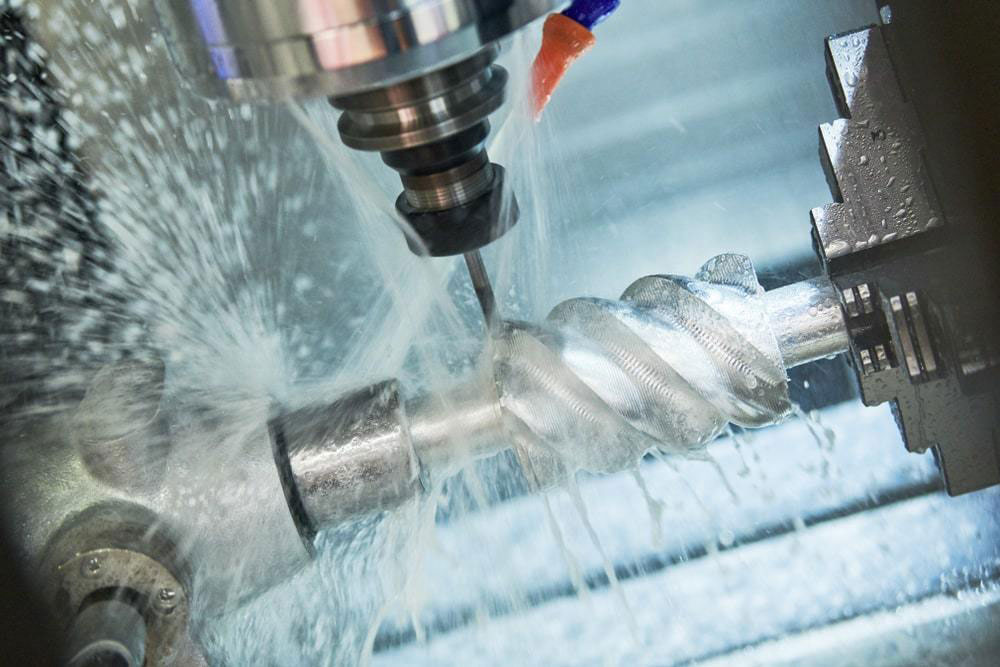
분명히 공구의 가공 용량을 초과하면 공구가 손상될 수 있습니다. 플런지 밀링의 경우에도 마찬가지입니다. 칩을 홈 바닥에서 제때에 배출할 수 없으면 칩이 압착되어 나중에 공구가 손상됩니다. 결론적으로, 이러한 조건은 초합금을 밀링할 때 공구 수명에 해롭습니다. 이송 속도를 늦추면 공구 수명이 늘어날 것이라고 생각했다면 그것은 착각이었습니다. 전형적인 예는 첫 번째 절단이 이루어졌을 때 재료가 매우 단단하다는 것을 발견하는 경우입니다. 이송이 감소하면(예: 인덱서블 밀링 커터의 날당 이송이 0.025~0.5mm로 감소) 공구의 절삭날이 가공물을 강하게 마찰시켜 공구가 손상될 수 있습니다. 빨리 또는 즉시. 마찰로 인해 공작물 표면이 경화될 수 있습니다. 가공경화를 방지하기 위해 첫 번째 칼날을 절단할 때 일정한 절단하중(0.15~0.2mm/날당 이송)을 유지해야 합니다.
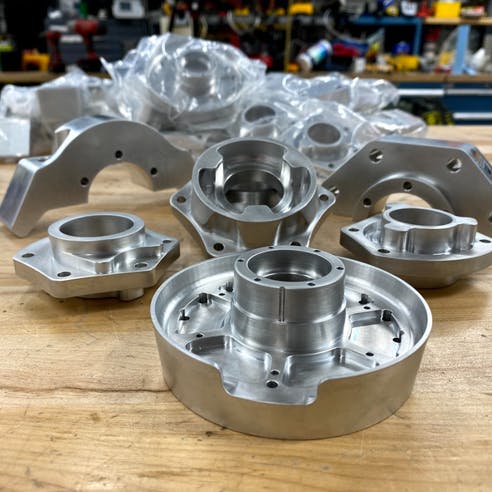
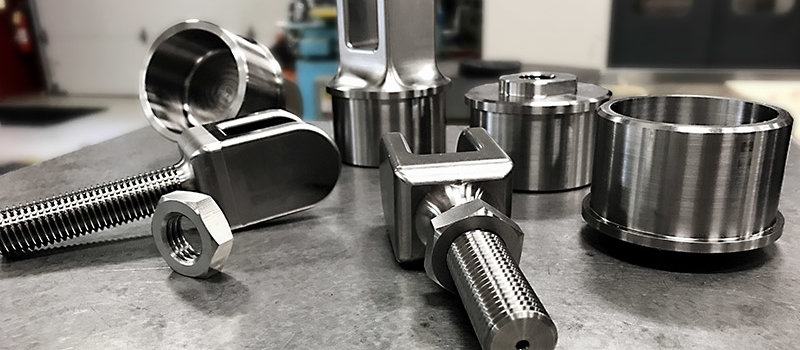
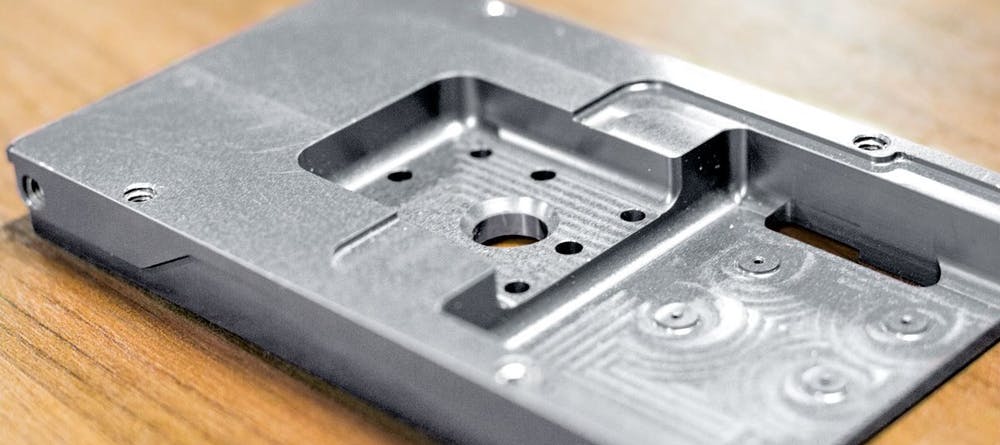