기계가공 생산과정에서 생산물의 형상, 크기, 위치, 성질 등이 변하여 완제품 또는 반제품이 되는 과정을 기계가공 공정이라 한다.
가공 공정은 주조, 단조, 스탬핑, 용접, 가공, 조립 및 기타 공정으로 나눌 수 있으며, 기계 제조 공정은 일반적으로 기계 가공 공정의 일부와 기계 조립 공정을 말합니다.
기계 가공 프로세스의 공식화에서는 여러 프로세스를 거치는 공작물과 프로세스 순서를 결정해야 하며, 주요 프로세스 이름과 프로세스 경로로 알려진 간단한 프로세스의 처리 순서만 나열해야 합니다.
공정 경로의 공식화는 공정 공정의 전체 레이아웃을 공식화하는 것이며, 주요 임무는 각 표면의 처리 방법을 선택하고, 각 표면의 처리 순서와 전체 공정의 수를 결정하는 것입니다. 프로세스 경로 공식화는 특정 원칙을 따라야 합니다.
가공 부품의 공정 경로 초안 작성 원칙:
1. 첫 번째 처리 데이텀: 후속 프로세스 처리를 위한 정밀한 데이텀을 가능한 한 빨리 제공하기 위해 위치 결정 데이텀 표면으로서 처리 과정에 있는 부품을 먼저 처리해야 합니다. 이를 "먼저 벤치마킹"이라고 합니다.
2. 분할된 처리 단계: 표면의 처리 품질 요구 사항은 처리 단계로 구분되며 일반적으로 거친 가공, 반 마무리 및 마무리 세 단계로 나눌 수 있습니다. 주로 처리 품질을 보장하기 위해; 장비의 합리적인 사용에 도움이 됩니다. 열처리 공정의 준비가 용이합니다. 또한 빈 결함 발견도 용이합니다.
3. 구멍 후 첫 번째 면: 상자 본체, 브래킷, 연결봉 및 기타 부품의 경우 첫 번째 평면 가공 구멍을 가공해야 합니다. 이러한 방식으로 평면 위치 지정 가공 구멍은 평면 및 구멍 위치 정확도를 보장할 뿐만 아니라 구멍 가공 평면에서도 편리함을 제공합니다.
4. 마무리 처리: 주 표면 마무리 처리(예: 연삭, 호닝, 미세 연삭, 압연 가공 등)는 공정 경로의 마지막 단계에 있어야 하며 Ra0.8um 이상의 표면 마무리 처리 후 약간의 충돌이 발생합니다. 일본, 독일 등의 국가에서는 가공을 마친 후 플란넬을 사용하여 표면을 손상시킬 수 있으며 손으로 공작물이나 기타 물체에 직접 접촉하지 마십시오. 공정 간 환적 및 설치로 인해 마감 표면이 손상되지 않도록 보호합니다.
가공 부품의 공정 경로 초안 작성을 위한 기타 원칙:
위는 프로세스 배열의 일반적인 상황입니다. 일부 특정 사례는 다음 원칙에 따라 처리될 수 있습니다.
(1) 가공 정확도를 보장하기 위해 황삭 가공과 정삭 가공을 별도로 수행하는 것이 가장 좋습니다. 황삭가공으로 인해 절삭량이 많고 절삭력, 조임력, 열, 가공면에 의한 가공물의 가공경화 현상이 크고 가공물의 내부응력이 크고 황삭가공이 계속되면 가공물의 내부응력이 커진다. 응력 재분배로 인해 마감 부품의 정밀도가 빠르게 손실됩니다. 가공 정확도가 높은 일부 부품의 경우. 거친 가공 후 마무리하기 전에 저온 어닐링 또는 시효 공정을 마련하여 내부 응력을 제거해야 합니다.
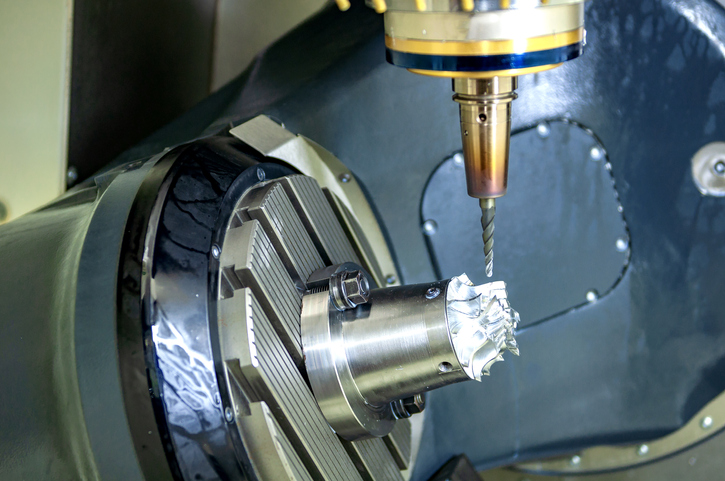
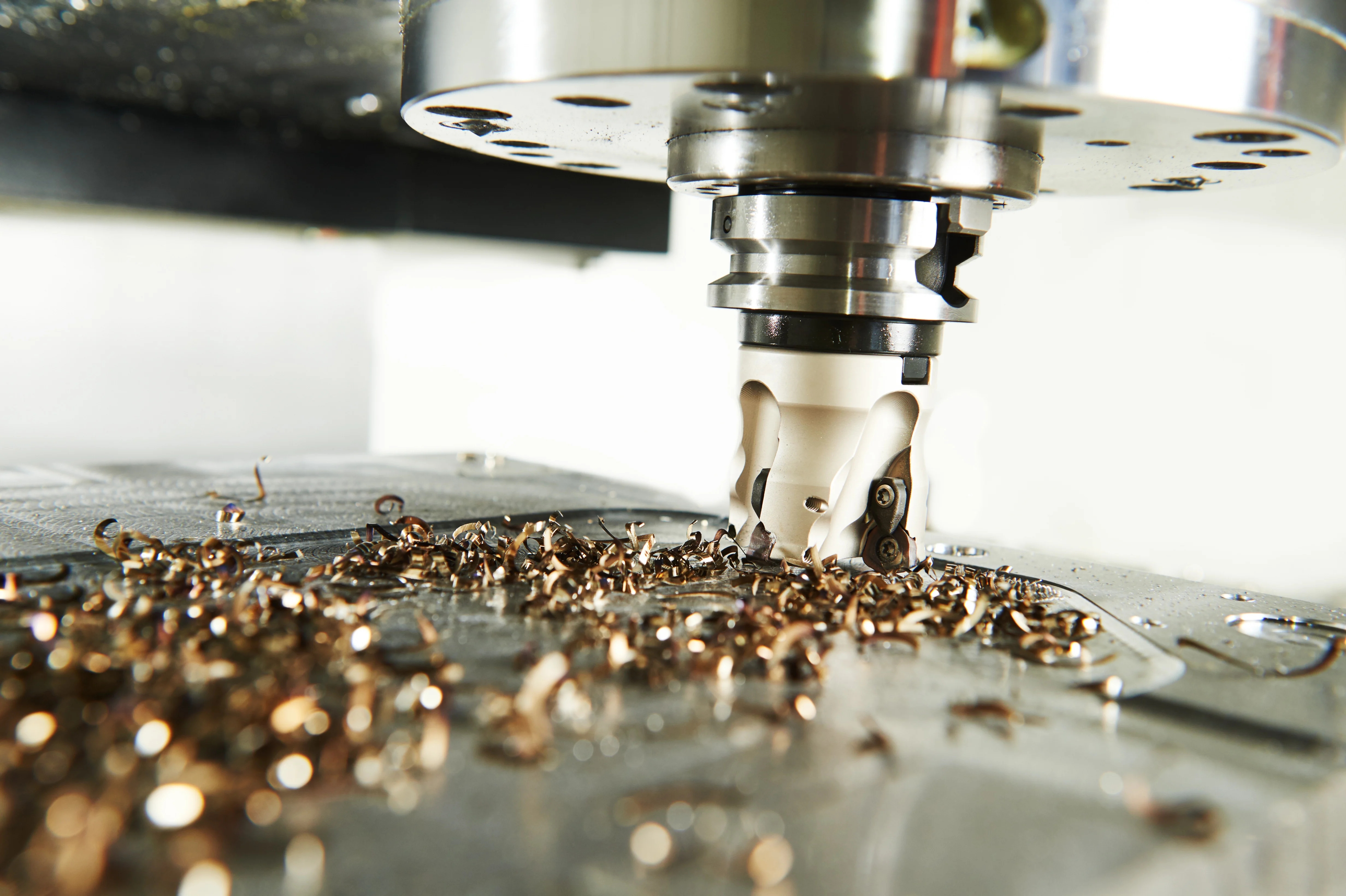
(2) 열처리 공정은 기계 가공 공정에 배치되는 경우가 많습니다. 열처리 공정의 위치는 다음과 같이 배열됩니다. 어닐링, 노멀라이징, 담금질 및 템퍼링 등과 같은 금속의 가공성을 향상시키기 위해 일반적으로 가공 전에 배열됩니다. 시효 처리, 담금질 및 템퍼링 처리, 거친 가공 후 마무리 전 일반 배치와 같은 내부 응력을 제거합니다. 침탄, 담금질, 템퍼링 등과 같은 부품의 기계적 특성을 향상시키기 위해 일반적으로 기계 가공 후에 배열됩니다. 더 큰 변형 후에 열처리를 하는 경우 최종 가공 공정도 준비해야 합니다.
(3) 합리적인 장비 선택. 황삭 가공은 주로 가공 허용량의 대부분을 차단하고 더 높은 가공 정확도를 요구하지 않으므로 황삭 가공은 더 큰 힘을 가해야 하며 공작 기계의 정밀도는 너무 높지 않으며 정삭 공정에는 더 높은 정밀도의 공작 기계가 필요합니다. 처리. 황삭 및 정삭 가공은 다양한 공작 기계에서 처리되므로 장비 성능을 최대한 발휘할 수 있을 뿐만 아니라 정밀 공작 기계의 수명도 연장됩니다.
부품 가공 프로세스를 작성할 때 부품의 생산 유형이 다르기 때문에 추가 방법, 공작 기계 장비, 클램핑 측정 도구, 작업자의 블랭크 및 기술 요구 사항이 매우 다릅니다.
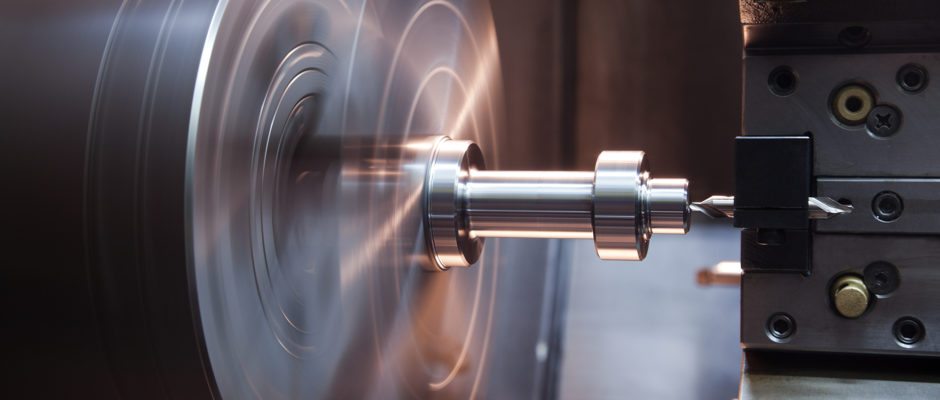
게시 시간: 2021년 8월 23일